Renault 5 GTT Frequently Asked Questions
contributed by Rich Russell
Common questions and answers. Please read this before asking questions on the board, as you may find the answer here, and save yourself abuse from the regular posters...
What is the 'cup mod' and what does it do?
The 'cup mod' comes from the circuit racing series called the 'Renault 5 Turbo Cup', which ran in the late 1980s. It involves simplifying the boost control pipework to improve turbo response. Roughly speaking, it consists of connecting the front actuator port to the carb base (rather than carb inlet plenum), disconnecting the rear actuator port, and blocking the ports in the exhaust elbow and carb inlet plenum. It has the advantage of neatening the engine bay by removing a load of pipes, but may lead to premature actuator failure or poor boost performance in very cold or hot weather.
See this diagram
 
All about the cup mod
What's a dump valve?
A dump valve or DV, also known as a Blow Off Valve or BOV, is fitted in the main boost hose from the intercooler to the carb. It's purpose is to, when the throttle is closed quickly, vent off the compressed boost air to prevent long term wear or at very high boost sudden damage to the turbo also to prevent momentary over fuelling on cars that use an air flow meter. Sometimes people find it can reduce the time taken for the boost to build after a gear change but mostly people find it increases the time. It works by having a diaphragm or piston or two that's pulled open by the vacuum formed in the inlet manifold when the throttle is shut. A spring holds it shut when the throttle is open. It also makes a nice 'ptcsssshh' noise!
Remember that Renault chose not to fit one as standard on the GT Turbo, yet most manufacturers do fit them as standard equipment (recirculating type) on turbocharged cars. The R5/R11 Turbo has quite a long boost path with reasonably wide hoses, so most pressure waves from the throttle shutting quickly are absorbed in the hoses, so you don't get the turbo damaging effect seen in cars with shorter paths. Hence a lot of people feel there's no need for a dump valve on a R5 GT Turbo or R11 Turbo.
How to fit a dump valve
Piston or Diaphragm dump valve?
There are two main types of DV - one uses a flexible diaphragm made from rubber or kevlar to seal the boost hose, the other uses a plastic or metal cylinder. Both work in the same way, the piston or diaphragm being pulled up against spring pressure by the vacuum. Diaphragms are prone to splitting eventually, but pistons can suffer from lack of lubrication and jam. The BOVs have a second seal also held by a spring. When the vacuum pulls the main seal open the second one remains shut unless there is a boost pressure in the main boost hose of higher pressure than the spring can hold when the second seal is then blown open and partial venting occurs. The system remains partially pressurised. Cars with air flow meter may not idle with a DV and need the BOV with it's closed at idle feature.
What's a bleed valve and where does it go?
A bleed valve is put in the pipe that controls the actuator on the turbo to make it open the wastegate at a higher pressure than it would normally do so. This results in the boost pressure produced by the turbo being higher. It works by literally 'bleeding' off a portion of the air, so that the actuator gets a lower pressure than there is at the carb top. It goes in the pipe that goes from the carb top to the front port on the actuator. Normally it's fitted under the bonnet, but there is a version that you can mount on the dashboard (ie with long pipes), so you can increase the boost when you need it (eg for overtaking), and drop it back down to normal for normal running. However it's recommended that you fit a limiter to prevent you opening up the valve beyond a safe limit.
How do you fit a boost gauge?
A boost gauge is best connected by cutting the pipe that runs to the ignition module (ECU) and inserting a T-piece in it. Then run a pipe from here to the gauge. This will give you negative readings (ie vacuum) as well as positive boost measured at the manifold (ie what the cylinders are receiving). The standard boost gauge measures from the top of the carburettor, which will be a few psi higher than below it.
What does 1 Bar equate to in psi?
1 Bar = 14.7 psi.
What is the maximum boost on standard turbo?
Standard maximum boost pressure is about 10psi, on the standard Garrett T2. You can raise this to 15 or 16psi without shortening the life of the turbo too much, but any more than that will seriously shorten it's life, or risk engine damage.
What is the maximum boost a standard intercooler can manage?
The standard intercooler doesn't cool very effectively above 14psi. It's also prone to blowing apart at 16psi or more. An alloy version will perform well up to around 30psi. Larger intercoolers which may have to be mounted in other places can cool more effectively.
What is strapping and flowing of the intercooler?
The standard intercooler has plastic top and bottom parts and an aluminium core. At boost pressures over 14psi, it's not uncommon for the plastic parts to come off due to the pressure. So you strap the intercooler with a large jubilee clip to hold them on. You can use one long strap (like plumbers use on boilers), or a few shorter ones joined together (easier to get hold of). The standard intercooler also has a flap in the top part that bypasses the intercooler core if the air is cold. This mechanism can push open at high boosts, and also is undesirable on modified cars - so simply remove the thermostat mechanism and glue the flap in place so that the air is always forced through the core. Some people have reported that a strapped and flowed intercooler has been tested at 26psi and didn't leak. Though this probably depends on how well it's converted. Also this is 26psi at the intercooler, ie, at the turbo, NOT 26psi at the manifold in which cae the turbo will be producing considerably more.
Cheap front mount intercooler options
Swapping over your intercooler
What is a chargecooler? Is it better than an intercooler? How do they both work?
An intercooler and a chargecooler both serve to cool the hot pressurised air from the turbo before it's fed to the carburettor. Cooler air is more dense, so contains more oxygen per unit volume. The intercooler does this by passing air over vanes much like a radiator does to cool the coolant. A chargecooler does the same, but uses water instead. A chargecooler hence also needs a pump and a radiator to dump this heat elsewhere. In theory, a chargecooler can remove up to four times as much heat as an intercooler of the same size. However a bigger intercooler is often cheaper and less complex to implement. Also whilst water may be more efficient at removing heat from the charge, it has two drawbacks. One is that water is heavy and two is that water takes a long time to cool down once heated. Therefore if you almost constantly use the boost then an air to air front mounted intercooler will be more efficient than a chargecooler. It would seem that charge coolers are good for a 'quick spurt' of power in the urban environment where their large themal mass acts as a larger heatsink, absorbing the heat from the 'short burst'. After perhaps 30 seconds they have warmed up. This is the same for an intercooler but the latter has less heatsinking ability. After that it's about efficiency as an ongoing cooling mechanism and here size matters. See this link: http://www.autospeed.com/A_0527/P_1/article.html
What torque do I do the head bolts up to?
If you're running standardish boost (9-12psi), and using standard head bolts and a standard head gasket, you should stick to around 60Nm. If you're running more boost, with an uprated gasket and 12.9 high tensile bolts, you can go to 75Nm. If you try to take standard bolts to this torque, they'll probably snap, and aren't easy to get out of the block. By bolting the head down tighter, you ensure that the gasket won't start to leak at high boost pressures.
How does the Turbo work?
The turbocharger is basically just a fan, powered by the exhaust gas from the engine. The exhaust gas goes through the manifold and into the turbine housing. In here it pushes a turbine round, then goes out to the exhaust pipe. Connected on the same shaft as the turbine, but in a different housing is a compressor. Fresh air from the air filter is drawn into the housing and pressurised by the compressor wheel, and then pushed out the exit hose to the intercooler. Obviously the more air you force into th engine, the more power it makes, and the more exhaust gas it makes, so some method of limiting the speed of the turbine/compressor is needed to prevent it breaking. This is done by having a hole from the turbine housing to the exhaust pipe, covered by a flap. This flap is normally shut, but can be opened by the actuator to allow gas to bypass the turbine. The actuator is just a diaphragm and spring that is pushed by boost pressure (usually measured at the carb top) to push a rod connected to the wastegate to open it. So boost pressure increases as the engine produces exhaust, up to a point determined by the length of the actuator to wastegate arm before the wastegate opens and exhaust bypasses the turbine. Now the turbine slows down, boost decreases, and the wastegate shuts. This happens very quickly so all you see is the boost rise to a certain value and go no higher. Turbo's obviously need a certain amount of gas to push the turbine, so at low revs it's not spinning and producing boost. On a standard GTT you will hear the turbo start to spin around 2000rpm, and be producing full boost by 3000rpm. Altering the exhaust and air filter will change these values, so you may get it producing full boost at 2000rpm.
How to replace your turbocharger
What is wastegate flutter?
This occurs at high boosts when the wastegate is forced open by the exhaust gases, leading to unstable boost. Generally fitting a stronger actuator solves it. It's also symptomatic of not having a dump valve that can vent the pressure fast enough.
What does pinking sound like?
'Like a bag of marbles being dropped onto a metal floor' is one description. Basically a metallic tinkling noise. If you hear it, back off the power, otherwise serious damage can result to the pistons and head (pitting, holes, cracks). Check you are using high enough octane fuel, have your carb set up to fuel adequately for the boost pressure you're running, and the engine's not too hot.
What size carb jets should I fit?
Standard carbs contain a 1.2mm (120) main jet and 1.25mm (125) air corrector jet. For up to 16psi, you should fit a 1.3 main jet, and possibly reduce the air corrector to 1 mm. This will ensure enough fuel can be supplied for the extra boost air supplied. Above 16psi, you will need to look at second stage enrichment. But take care not to over fuel because this can cause bore wash and rapid wearing of the piston rings and cylinder liners can result.
Changing the carb jets
What is the part number for a .90 corrector jet?
You can no longer get this from Renault easily. Racetek (see Contacts section for phone number) can supply them though, or you can adapt an existing jet by filling it with solder and drilling it out with a 0.9mm drill.
What is a Group A carburettor?
Whilst the GTT was never actually homologated for Group A (although the R11 was), several tuners like to use this term to describe a carb that has a wider venturi than standard, often 27.5 or 28mm compared to the standard 25mm diameter hole. It also often has no choke flap and will have larger (often 1.5mm) main jet, and smaller air corrector (often 0.9mm) and larger enrichment jet. This is similar to the carb used in the Turbo Cup series, and provides more boost in the manifold from that made by the turbo due to lower pressure loss and better control of fuelling at high boosts (>15psi). Below 15psi, there's not much to be gained, and you may find it overfuels badly. The turbo cup series were regulated to about 14psi. But reducing pressure losses means less heat is produced by the turbo as less boost is needed to make the 14psi, leading to greater system efficiency and also affording the possibility of increasing the timing advance.
All about the carburettor
What is carburettor icing, and how do I avoid it?
In cold, damp weather (eg freezing fog), you may suffer from carburettor icing. Particularly if you have an uprated (or flowed) intercooler, without the thermostatic flap, and if you have changed to a lower temperature thermostat in the cooling system.
Carb icing is caused when the moisture in the air is cooled by the fast moving air in the carb venturi, and turns to ice - partially blocking the venturi. Symptoms of carb icing are juddering or hesitation on acceleration, lack of power and ultimately stalling after running for a few minutes off boost without changing revs much (ie cruising at 60mph usually does it). The problem goes away if you sit in traffic or accelerate hard on boost, so the engine temp goes up.
Basically the air going into the carb is too cold. So you need to reduce the efficiency of your intercooler by blocking off part of it with a bit of cardboard (so less air can flow through the grille, and cool the inlet air). Also you might want to consider refitting a standard thermostat if you have a lower temp one - so the coolant gets hotter (but still keep it below the third line on the temp gauge).
What's the pipe that goes from the carb to nowhere for?
There is a pipe that leads from the side of the carb down the side or front of the gearbox, and just points at the floor. It's purpose is to maintain atmospheric air pressure to the back of a moving diaphragm in the enrichment device instead of it being sealed and so preventing the diaphragm moving fully. In case the diaphragm leaks, the pipe is there to convey the petrol away from the hot exhaust manifold directly under it. So don't unplug it or remove it.
Fuel pump relay module explained
What fuel is best to use?
The GT Turbo was designed for 97-99 RON leaded four star petrol in the UK. However, as leaded fuel wasn't present in all the places it's sold, it's probably safe to use unleaded without any significant damage to the valve seats occurring. The main problem is the octane (RON) rating. You should use 98RON Super Unleaded, 99RON Shell Optimax or 98RON leaded four star. If you're stuck, a fiver's worth of 95RON Premium Unleaded will get you to somewhere that sells Super or Optimax, but due to it's lower octane running Premium Unleaded will cause engine damage if used on boost for any length of time. Stay well away from Lead Replacement Petrol (LRP) - although it's octane rating is good, it contains lead substitutes that attack the turbo internals due to the high temperatures there.
What oil shall I use?
A good choice is polyolefin oil such as Mobil 1 0W40 or 15W50. Ideally use a fully synthetic oil as these provide better stability at high temperatures. But if you've always used a non synthetic, changing could cause residue to dislodge and possibly block the tiny oil ways in the turbo.
More about choosing your engine oil
Changing your engine oil
A thread on "Is this oil pressure OK?"
How does the breather system work?
Manifold vacuum is used to suck the oil vapour from the rocker cover, mixed with clean air from the filter. The main purpose is to keep the inside of the engine (crankcase, rocker cover etc) at a lower pressure than outside the engine, so the oil seals and gaskets don't leak oil into the environment.
There are obviously refinements on some cars, such as the separator pot on the GT Turbo that helps return liquid oil droplets to the sump, and the one way valve that stops it blowing from the manifold into the rocker cover when on boost (not a good idea!). Under boost conditions, the vapour is sucked into the turbo inlet by the air rushing from the filter. Not ideal, but it's got to go somewhere...
It relies on the vapour being sucked by the manifold. A small amount of air is mixed to ensure that the vapour burns properly in the cylinders. The amount of vapour and air is controlled by the restrictors in the pipes.
You can fit a small filter instead of the connection to the air filter hose - which will prevent oil vapour going into the turbo. However, as the small filter won't provide the 'suck' that the fast flowing air into the turbo does, the breather system won't work as well. But well enough for a well maintained engine. The filter will almost certainly get clogged with oil eventually though, and need cleaning.
You can also put a catch can in to prevent any oil vapour reaching the manifold at all- again, relying on the pressure in the rocker and crankcase to get the vapour out. Not as effective as the standard setup, but prevents any problems due to oil going into the intake.
Oil catch tank, do you need one?
If your car is blowing oil then yes, if not no.
Some people remove the breather system and in it's place just have a filter on the rocker but usually some oil comes out of this. Or they pipe the rocker to a bottle or catch tank. Some are more sophisticated and called oil separators, they swirl the oil mist that is leaving the rocker cover / crank case and the oil collects and drains back to the sump. The 5GTT already has one of these fitted, the swirl pot above the water pump, but there is a limit to how much it can cope with. There are larger versions available to cope with more mist.
It seems that the breather pipes that go to the manifold are there to reduce emissions as having some oil vapour going into the combustion reduces nitrogen oxides, or something, so that's good. Not required for track cars.
It's best to have good crank case breathing or the oil leaks out from the oil seals and maybe past the piston rings and cause smoke from the exhaust and excessive oil consumption.
What's the best way to start modifying?
Opinions vary - but assuming you have a totally standard GT Turbo, here's some pointers on how to start. Lower the suspension a bit to improve handling. Replace the exhaust with a performance system, and upgrade the air filter at the same time. This should give you a bit more torque. Fit a boost gauge so you can see what's going on, and a bleed valve to increase the boost up to 12psi. This should give you a noticeable increase in power. Now it's time to change the carb jets to allow more fuel, and increase the boost to 15psi. You will need to strap/flow the intercooler at this point too. Changing the rad fan switch temperature sensor for a lower temperature one keeps the running temperature a bit cooler but not too much cooler. By now you should have a reliable 150bhp. Beyond this, it's up to you! Aim for 200bhp, but you'll have to start spending money to reach it....
How much is insurance?
Depends on your age etc, but you should be able to get under £600 if you're over 25. At age 18, you're looking well over £1500 in most cases. Some insurers now consider the GT Turbo a 'classic', so if you're of the right age, they'll put it on a Classic Car insurance policy, which is much cheaper - but usually with quite restricted mileage allowance.
What size wheels fit?
Standard are 13" with 195/55 tyres. Any increase in wheel diameter must be countered by a corresponding reduction in tyre depth. So 15" wheels with 195/45 tyres will fit, and the speedo will be correct still. Offset is 35-40mm, depending on wheel size.
What things should be regularly checked to avoid major problems?
Check the oil level is above halfway. Check oil pressure is 4 Bar when driving, and around 1 Bar at idle. Check temperature doesn't go above 60% for any length of time. Check coolant is above minimum. Check boost pressure doesn't go over what you know is safe for your engine.
What does polishing and porting the head mean?
The head is made of cast aluminium alloy. The casting leaves restrictions, rough edges and marks in the passageways that the gases flow through to and from the valves. You can have the casting smoothed to remove these, which improves the ease with which the gases flow. Generally you don't smooth the inlet ports all the way to a polished finish, as the roughness helps mix the petrol and air. Porting means to widen the passageways as much as possible without leaving the walls between them weak. By having bigger ports, more gas can flow in and out of the combustion chamber leading to more power. However this can also have an adverse effect at lower gas velocities, ie, low rpm, as lowering the gas speed further by widening the ports can mean the chamber can fill less making less power. The same is true with widening the throats and also fitting bigger valves.
How does a performance camshaft help?
The camshaft controls the opening and closing of the valves that allow fuel/air in, and exhaust out of the cylinders. The standard cam profile is designed to be a good compromise between smooth running and power. If you're prepared to sacrifice a bit of smoothness, big gains in power can be achieved by using a camshaft with different opening and closing timing, and valve lift.
What spark plugs should I use?
NGK B8EVX are currently the most popular, although you may need a different plug if your engine doesn't perform well with these. Also the B8EG works well. These are both avaliable in B9 for a colder plug. Some people still favour the Champion plugs.
What is, and do I need to keep my anti-percolation fan?
This is the fan that runs on for up to 30 minutes or so after switching the engine off. It's purpose is to blow cool air at the carburettor, and through the boost hoses to prevent the petrol in the carb evaporating and help keep the intercooler and turbo compressor relatively cool. Without it, you may find starting the car after a hot run difficult, as the carb contains no fuel, or the fuel contains bubbles of vapour. If you improve the general cooling of the engine, you can safely remove the anti-perc system in many cases. Though some people have reported that without it their engine ran less well as soon as they reached traffic. This ceasing to be the case with the re-instatement of their anit perc. fan.
Which type of air filter, standard box filter or induction kit?
The standard air filter system is unusually well designed. It involves the air hitting the intercooler, and a lot of it being deflected upwards into a scoop. This is then funnelled down to a sealed metal cylinder containing the air filter. The output of this goes to the turbo. This system is known as a ram-air intake system, and ensures cold air is forced into the turbo, rather than just sucked. You can upgrade the standard paper element to a performance filter such as K&N. The other alternative is to remove all the ram-air system, and fit a cone shaped induction filter instead. This has the advantage of a shorter pipe run, and so can improve the response of the engine. However, careful siting or ducting is needed to prevent it sucking warm air.
How do I bleed the air from my engine and cooling system?
You lift the header tank, with it's cap off, as high as you can, checking there's pleanty of coolant in it.
You undo the bleed nipple on the big water hose until water flows out then do up.
Undo the one on the small hose until water runs out then do up.
Start the engine.
Still with the tank high and with enough coolant in, undo the small hose nipple again. The remaining air in the engine and hoses should come out, eventually. Do up the nipple.
If you undo the large hose nipple with the engine running then air is probably going to go IN not out as, with the thermostat shut, there is suction in that hose as the pump draws the water out of it. If the water is hot enough to open the Stat then water MAY come out, or not.
If you're using silicon hoses then don't over tighten the nipples or they can start to leak from where the hose joins the metal of the nipple body. Sometimes the rubber O rings need to be changed. The club has a very small supply of these O rings from Samco.
What is the rear brake compensator?
It adjusts the amount of hydraulic pressure that gets to the rear callipers according to the weight in, therefore the height of, the rear of the car. It's there to stop the rear brakes from locking up but provide more braking effort when there's more weight over the rear wheels.
How are boost pressure/petrol octane rating/compression ratio/ignition timing related?
On a standard engine, standard compression, standard ignition, correct fuelling a reasonable intercooler and a T28 turbo, boost can be up to 27psi before it knocks. This has been repeated a couple of times on different engines.
For every degree of ignition advance, knock becomes apparent 1psi of boost earlier.
For every 0.1 increase in CR, knock becomes apparent 1psi earlier.
For every 1 point increase in fuel RON you can run an extra psi of boost.
so VERY roughly speaking:
1psi = 1degree = 0.1:1 cr = 1 RON.
these figures seem pretty constant amongst a lot of turbo cars.
| | 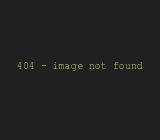
|